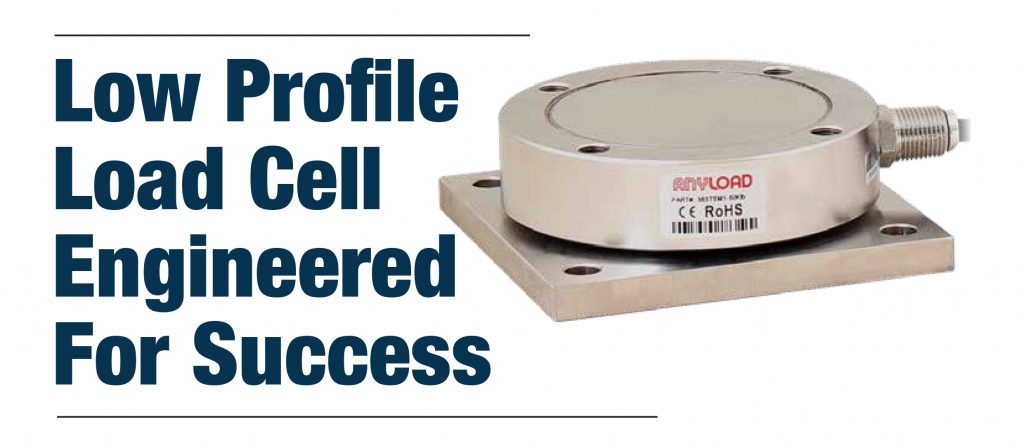
A few years ago, we received an inquiry from a scale company wondering if we had an interest in going above and beyond what the market was offering in a low profile, high capacity vessel, hopper, tank weigh module that does not need assembly before installation.
The Challenges:
The challenge consisted of a 50,000-pound capacity compression weigh module with a declared accuracy of 0.05 percent and the desired profile lower than 2.2 inches. This size would be about a quarter of what was common in a weigh module height of 8 inches. In the hopper and tank weighing sector of the process weighing industry, 0.1 percent is considered the high accuracy gold standard. Our Anyload engineers set out to improve the accuracy while remaining within the desired height constraint, or in this case, target.
Shrinking a conventional weigh module envelope design was not going to cut it. The Anyload team first sampled a few existing competitive contenders and identified key vulnerable areas needing improvement. One competing product fulfilling the low-profile requirement had only achieved an accuracy of 0.3 percent; hence, short of the target. Another key issue was repeatability (because of movement) of the load cell due to temperature or loading conditions during the actual weighing
The Result:
With these challenges in mind and keeping with our Anyload design philosophy of delivering austere and reliable products, we developed our first prototype.
Abandoning the spherical washer entirely, we internalized the applied force loading area with a spherical load pin. This allowed us to seal off the bottom of the load cell with a threaded and welded stainless steel ring, plus a rubber O-ring, thus improving the product’s reliability for wash down applications and keeping the uplift protection up to 50 percent of the capacity. Accuracy was much improved, even when there was a slight shift in the weight distribution or tilt to three degrees.
However, this design still faced the same challenge of achieving higher accuracy— although to a lesser degree. A fundamental weakness of our spherical load pin-load prototype (and that of our fellow manufacturer with their spherical washer load cell) was that any off-center load movement would still interfere with repeatability during weighing. It’s the shifting of the point-of-contact in the load introduction area that causes the interference. Variable loading conditions and temperature variations made this challenge unavoidable. Our initial prototype did not solve the problem of horizontal movement, which lead to poor repeatability.
We decided to abandon this spherical load pin approach in favour of a more novel approach and design. We flattened the top of the load pin. We implemented a protruding convex dimple with a concentrated radius centered on the load cell’s underside as the ideally focused load introduction area. Now, even with off-center applied loads, this elegant mechanical feature will better isolate the applied load to accommodate and provide a substantially more accurate reading. This design also reduced the overall size of the concentrated loading area, thus pinpointing precision. While our standard commercial model is promoted as having 0.1 percent accuracy, our extensive testing has found that this design is capable of 0.05 percent accuracy. At 50,000 pound capacity, we came below the ceiling of 2.2 inches with a total height of 2.09 inches. The Anyload solution has significantly improved accuracy and repeatability—all in all; it simply works better.
In two years of development, all of the capacities were created, and most of them are in stock at both our New Jersey and Vancouver warehouses, from 1,000 pounds to 200,000 pounds. For example, the total height of a 100,000-pound cell is 3.07 inches. Also, for ease of installation, we offer a top plate option for the weigh module. This provides a symmetrical bolt mounting pattern for the top and bottom. We rely on our customers and fellow competitors to provide the impetus for new products and improved designs. Rising to meet the challenge requires mutual inspiration and open minds. Our Anyload engineering team looks forward to continuing our industry-leading pioneering and forward-thinking. Patent pending for Europe and the USA.