Electric Car Battery Weighing
Load Cell for Battery Weighing
The weight of an electric car battery has a significant impact on the overall performance and efficiency of the vehicle. In the new energy electric vehicle industry, each battery pack used in electric cars must be monitored. The weight of a lithium battery affects the vehicle’s energy storage, acceleration, handling, and safety. Battery packs typically account for 20-30% of an electric vehicle’s total weight and are a core component. Variations in battery weight can significantly influence the vehicle’s energy efficiency and performance.
Challenge
- Dynamic Weighing: Since electric vehicles are produced on an assembly line, the entire weight monitoring process is dynamic, meaning the weighing occurs during movement. Therefore, the design of the weighing module solution must accommodate vibration (dynamic) applications.
- Eccentric Weight Correction: Due to varying pickup positions of the battery pack, the load positions on the sensor module are not always consistent, causing eccentric load distribution. The weighing module solution must include an eccentric weight correction function.
- Impact and Overload Resistance: With each weighing state change, the battery pack generates impact loads during the process, so the module design must meet impact and overload resistance requirements.
- High Precision: The weighing module solution must still provide high-precision, stable output under the above conditions.
Solution
Based on the size of the battery pack and the production environment, ANYLOAD offers customized solutions. We have provided dozens of effective solutions for EV battery pack manufacturers, one of which is showcased below.
- Eccentric Weight Correction Sensors: Sensors are designed with eccentric weight correction and undergo eccentric weight calibration during production.
- Shock-Absorbing Link Design: The sensor module solution uses four shock-absorbing links, which convert the dynamic weight of the battery pack into a single-directional weight that is easier to measure.
- Dual Overload Protection: A dual-layer overload protection design effectively ensures onsite safety.
Conclusion
Through discussions and evaluations of our clients’ production environments, we have developed a design most suited for their operational needs. The weighing module has been optimized with FEA modifications and features a multi-link shock-absorbing design, effectively preventing accuracy issues and unstable data caused by production conditions.
In both factory and onsite testing, ANYLOAD’s designs for various battery packs and production environments consistently meet customer requirements.
For more information, please contact ANYLOAD.
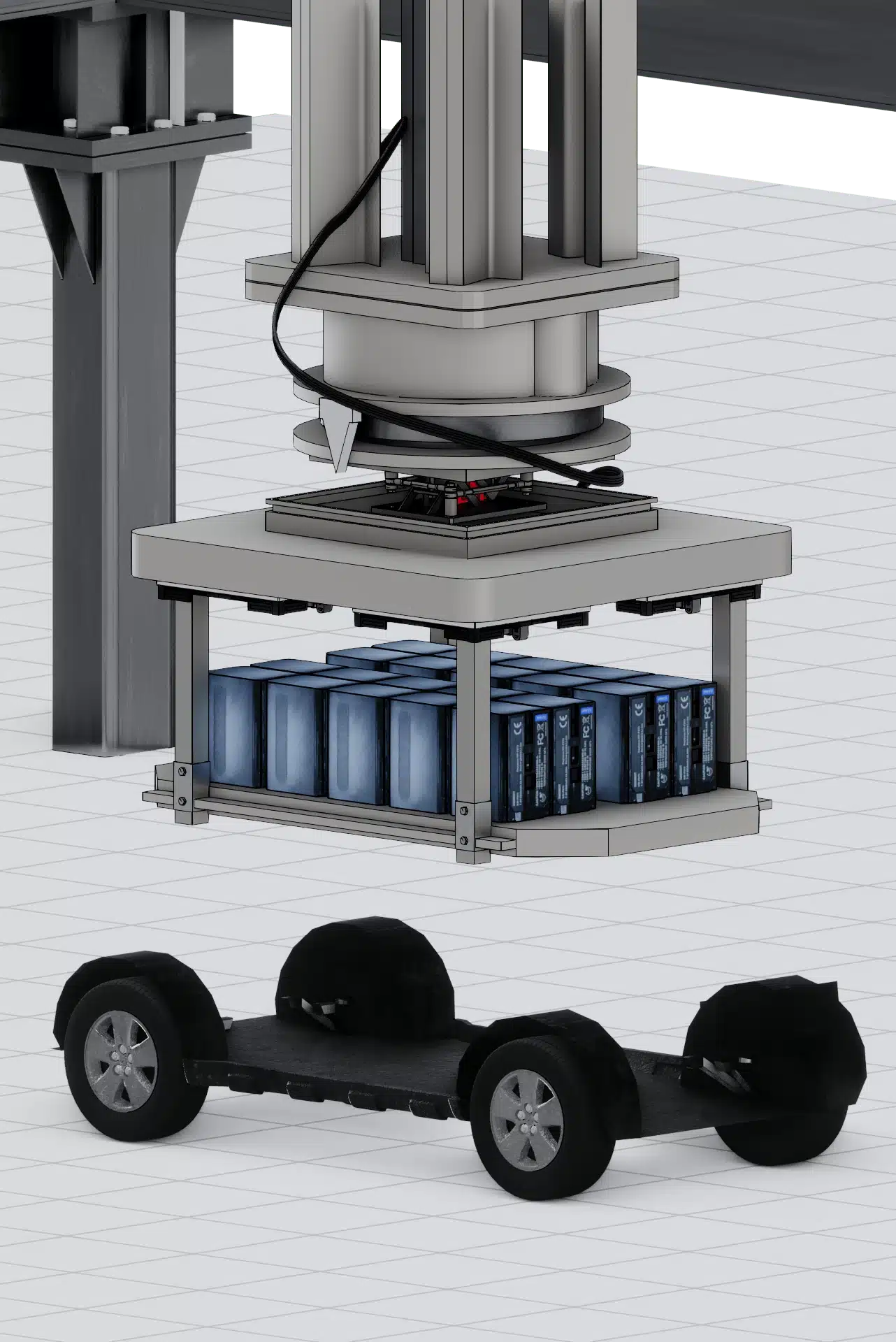
Featured Products
108DA
Single Point Load Cell
See standard version.
- Material: Aluminum, Clear Anodized
- Rated Capacities: 500kg, 800kg, 1t, 1.5t, 2t
- CE and RoHS certified
The 108DA is a heavy-duty single point delivering reliable performance for medium and high-capacity applications. Each load cell is individually adjusted to protect against corner errors. This model is a simple and easy-to-install solution and common applications include platform scales, floor scales, bench scales, check weighing, process weighing, hanging scales, and more. The 108DA is interchangeable with Vishay Tedea-Huntleigh 1320, Celtron HOC and Flintec PC81.
Agricultural Weighing Solutions
How agricultural industry uses our load cell for cart and mobile equipment for optimal result
Increase Turbine Life Span
Gravimetric quality assurance solution for wind turbine blades studies
Bag Filling Machine Load Cells
Bag filling and other process weighing and control system for maximal efficiency